Ключевые даты
В декабре 1962-го года, когда весь мир выдохнул из-за снижения напряженности, вызванной «Карибским кризисом», Совет Министров СССР принял постановление о создании на базе Государственного союзного опытного завода № 300 (тогда — ОКБ №300, сегодня — АМНТК «Союз») Специального конструкторского бюро турбохолодильных машин (СКБ ТХМ).
С инициативой об образовании филиала, где бы велась разработка воздушных и газовых турбохолодильных машин, выступили два первых руководителя ОКБ №300, конструкторы авиационных двигателей Алексей Микулин, Сергей Туманский, а также Борис Стечкин — дядя Игоря Стечкина, создателя знаменитого автоматического оружия.
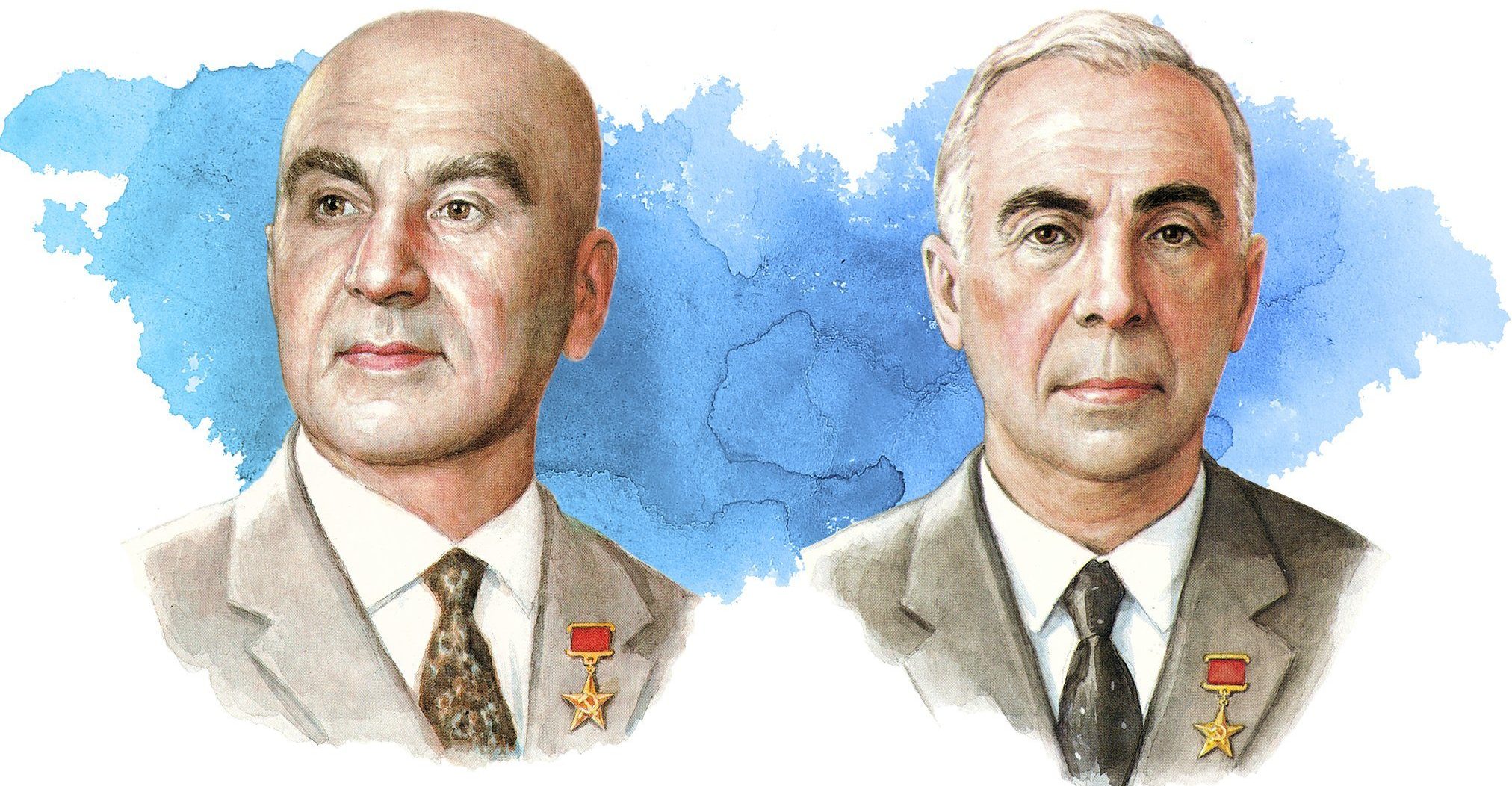
Конструкторы специального бюро проектируют, создают и успешно проводят испытания первой в Советском Союзе партии ТХМ. Впоследствии будет выпущено более 950 агрегатов широкого круга применения: от народного хозяйства и здравоохранения до атомной энергетики и военно-промышленного комплекса. Главная особенность – исключительная экологичность, благодаря отсутствию хлорсодержащих хладагентов, а также возможность получения сверхнизких температур
На базе СКБ ТХМ ММЗ «Союз» создается специализированная организация по проектированию и конструированию воздушных и газовых турбохолодильных машин. Новое подразделение входит в состав Главного Управления компрессорного и холодильного машиностроения при Министерстве химического и нефтяного машиностроения Советского Союза.
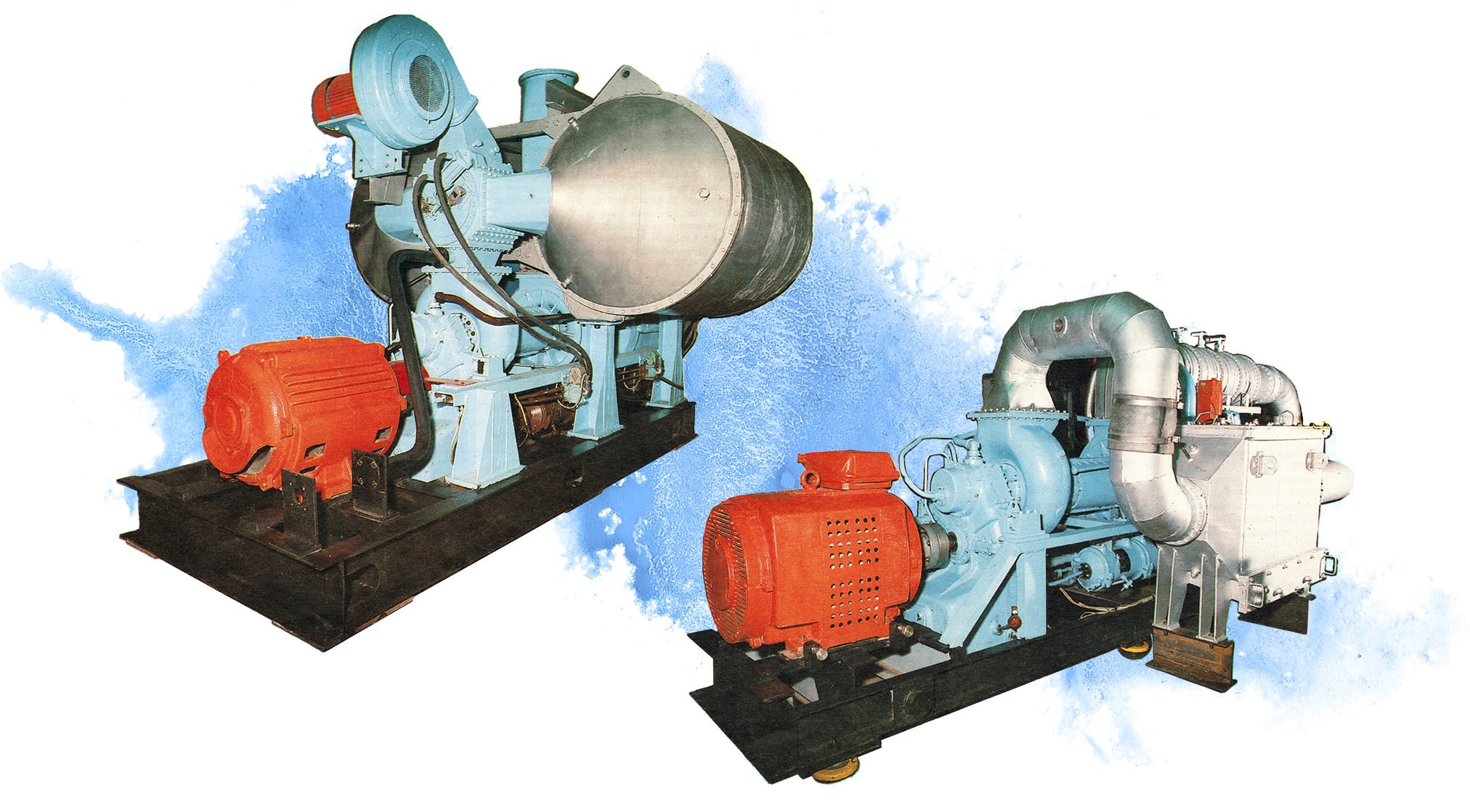
Минхимнефтемаш СССР назначает СКБ ТХМ головной организацией для проведения модернизации агрегатов для перекачки по магистральным трубопроводам природного газа (ГПА-Ц-6,3) и номенклатуры оборудования с повышенным сроком службы и надежностью.
В ранге головной организации Специализированное конструкторское бюро приступает к созданию газоперекачивающего агрегата нового поколения — ГПА-Ц-16, серийное производство которого начинается в 1980-м.
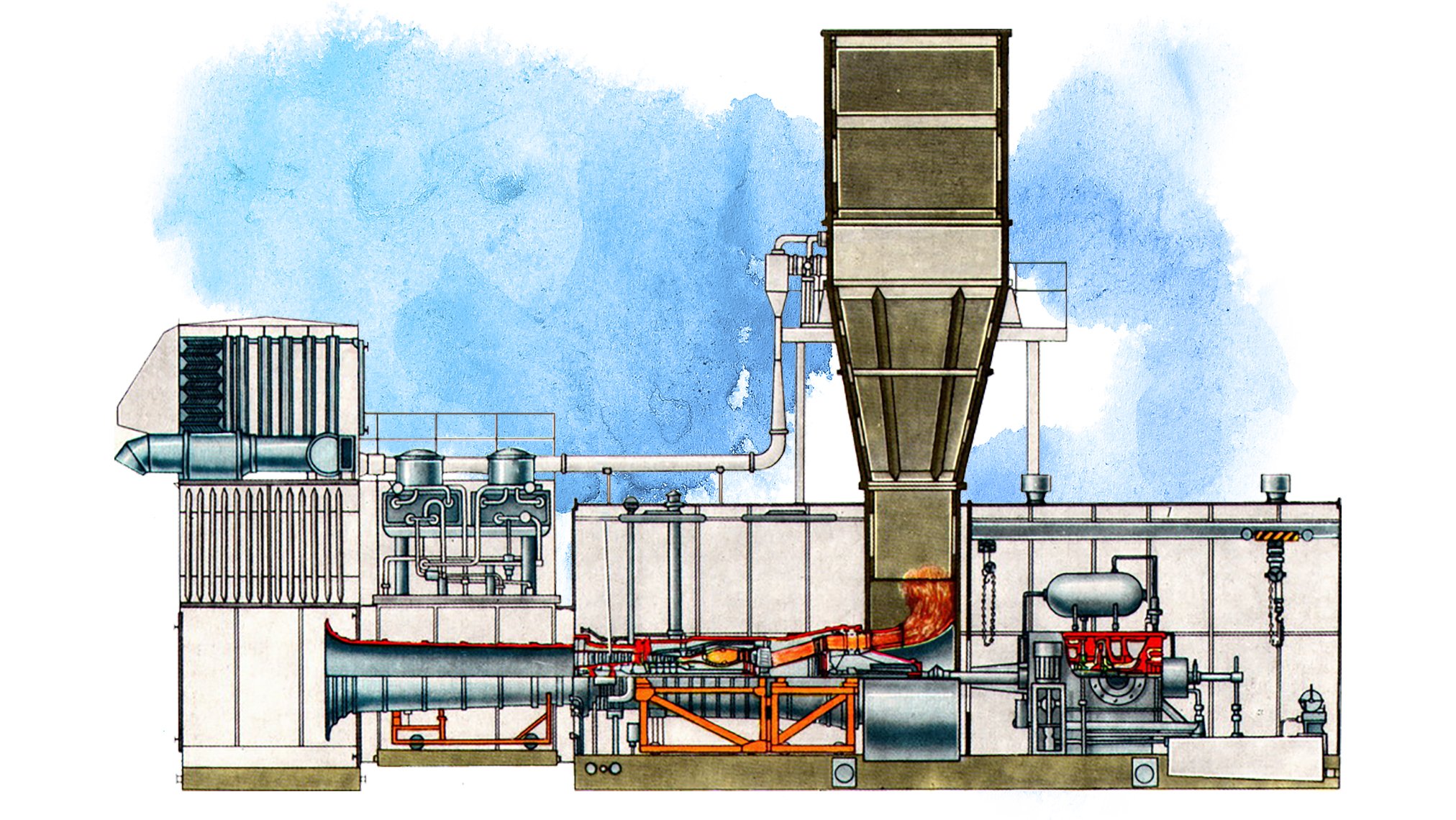
Машина ТХМ1-25 выставляется на международной выставке в г. Лейпциг, где получает высокую оценку экспертов и удостаивается Золотой медали и диплома 1-й степени. В это время на Родине конструкторское бюро активно работает над созданием и производством турбодетандерных агрегатов (ТДА). Оборудование для сепарации природного газа при низкой температуре применяется для добычи «голубого топлива» на газоконденсатном месторождении Машевское в Украинской ССР.
Вслед за освоением нового направления деятельности — автоматизация и микропроцессорная техника — СКБ меняет название на Специальное конструкторское бюро по автоматизации, микропроцессорной и турбохолодильной технике. После преобразования специалисты СКТБА разрабатывают турбодетандер с активным магнитным подвесом. Опытный образец агрегата поступает в «Ямбурггаздобыча».
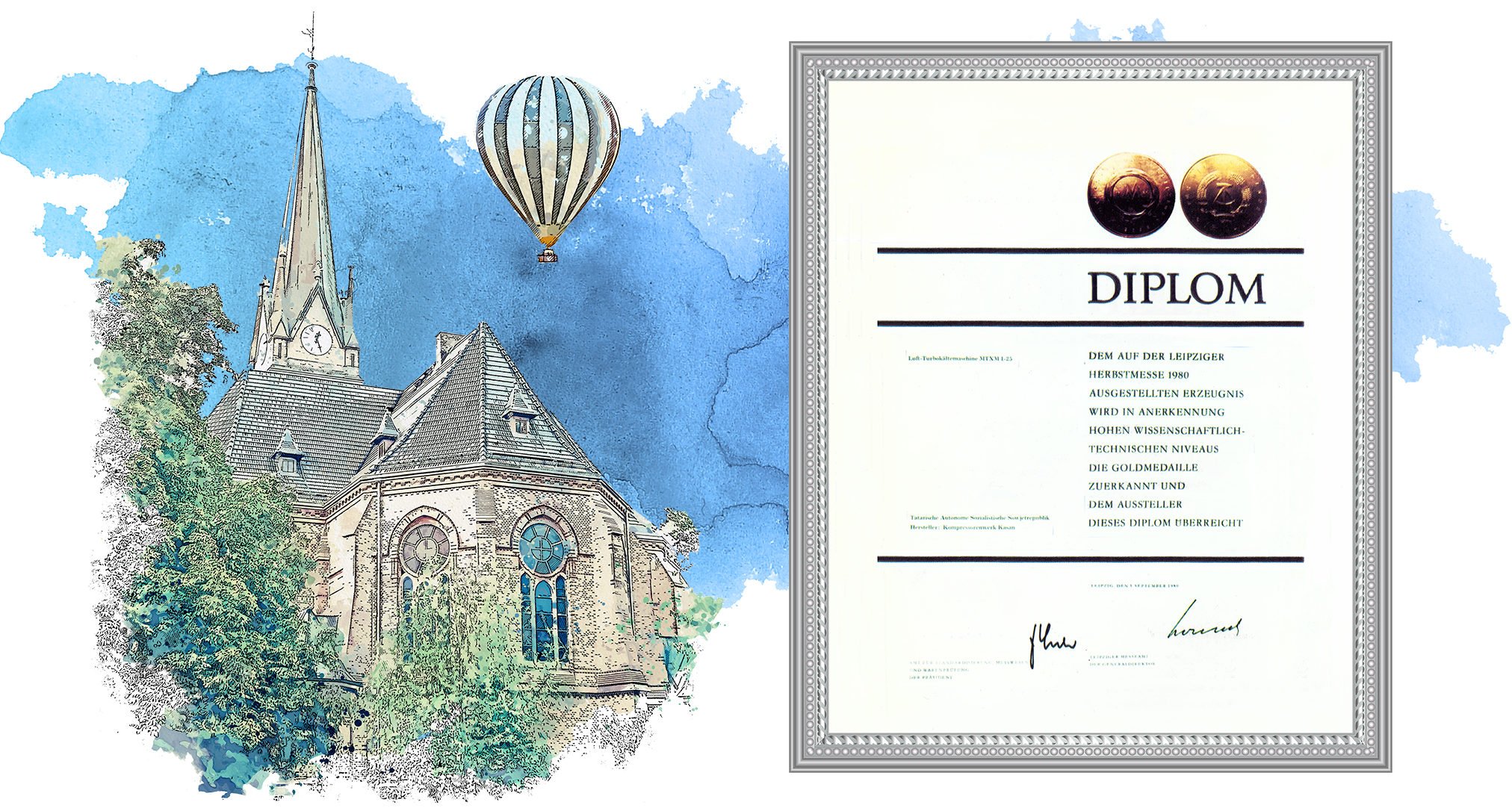
Завершена работа над ТДА для сжижения этана, которым оснащается Оренбургский гелиевый завод. Во Вьетнам и в США на экспорт поставляются турбохолодильные машины для предприятий, утилизирующих автопокрышки.
Уже в Российской Федерации приказом Министерства промышленности СКТБА переименовано в Специальное конструкторское бюро «Турбохолод», в 1993-м преобразованное в АООТ. ТДА с активным магнитным подвесом оснащается Установка комплексной переработки газа на месторождении Шуртан в Узбекистане, а в аэропорте г. Ташкента начинается эксплуатация турбохолодильной машины.
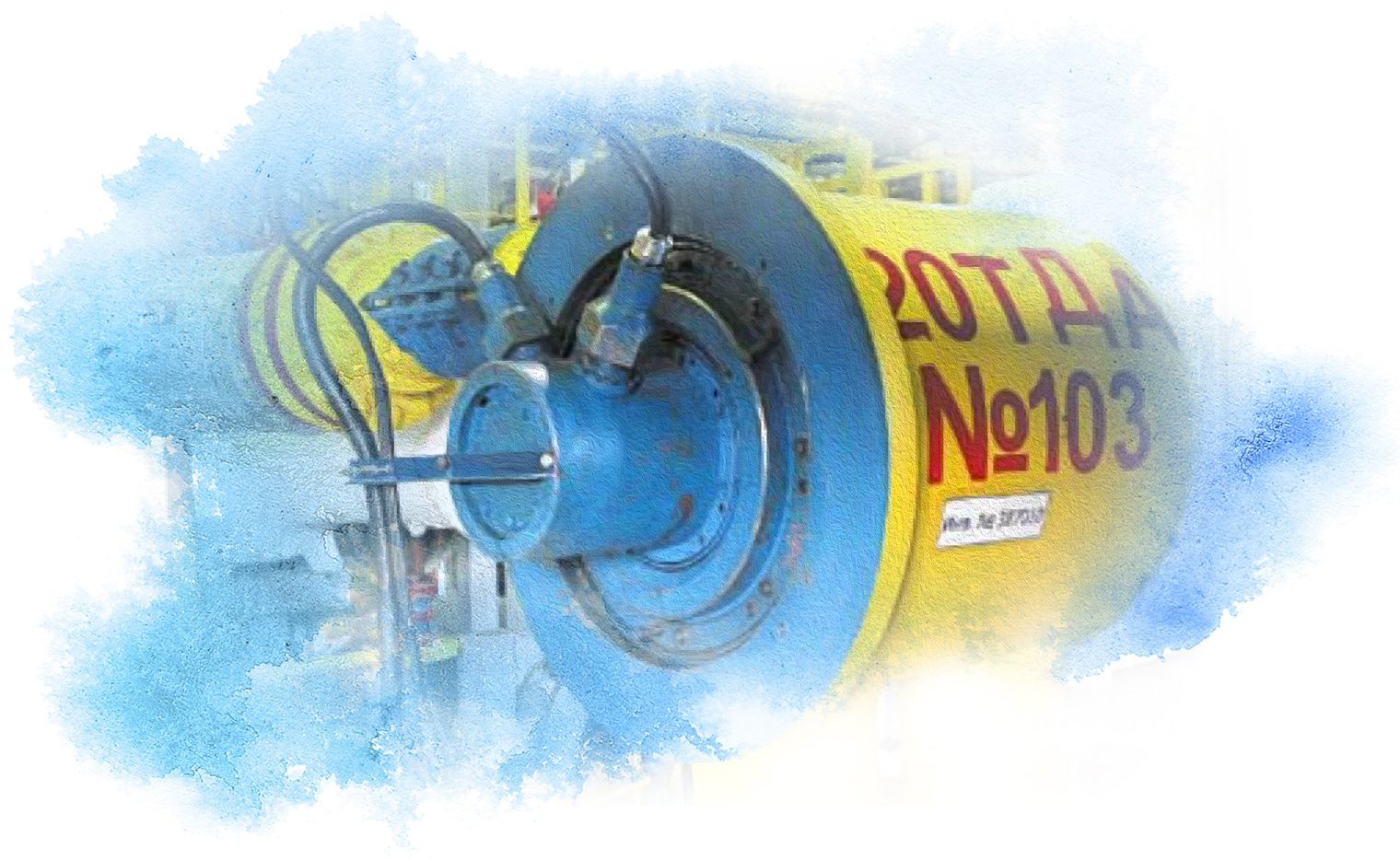
Начало совместной деятельности с ведущим в мире производителем подшипников, систем смазки и мехатроники — французской компанией SKF. Результатом совместной работы становится создание к 2002 году принципиально нового агрегата АДКГ-10 с активным магнитным подвесом SKF S2M. В том же году ОАО «Турбохолод» становится частью ГК «Меркурий».
«Турбохолод» полностью обеспечивает потребность российских добывающих компаний в ТДА для низкотемпературной обработки газа на головных станциях, и агрегатах, охлаждающих газ, перед транспортировкой в условиях Крайнего севера и вечной мерзлоты.
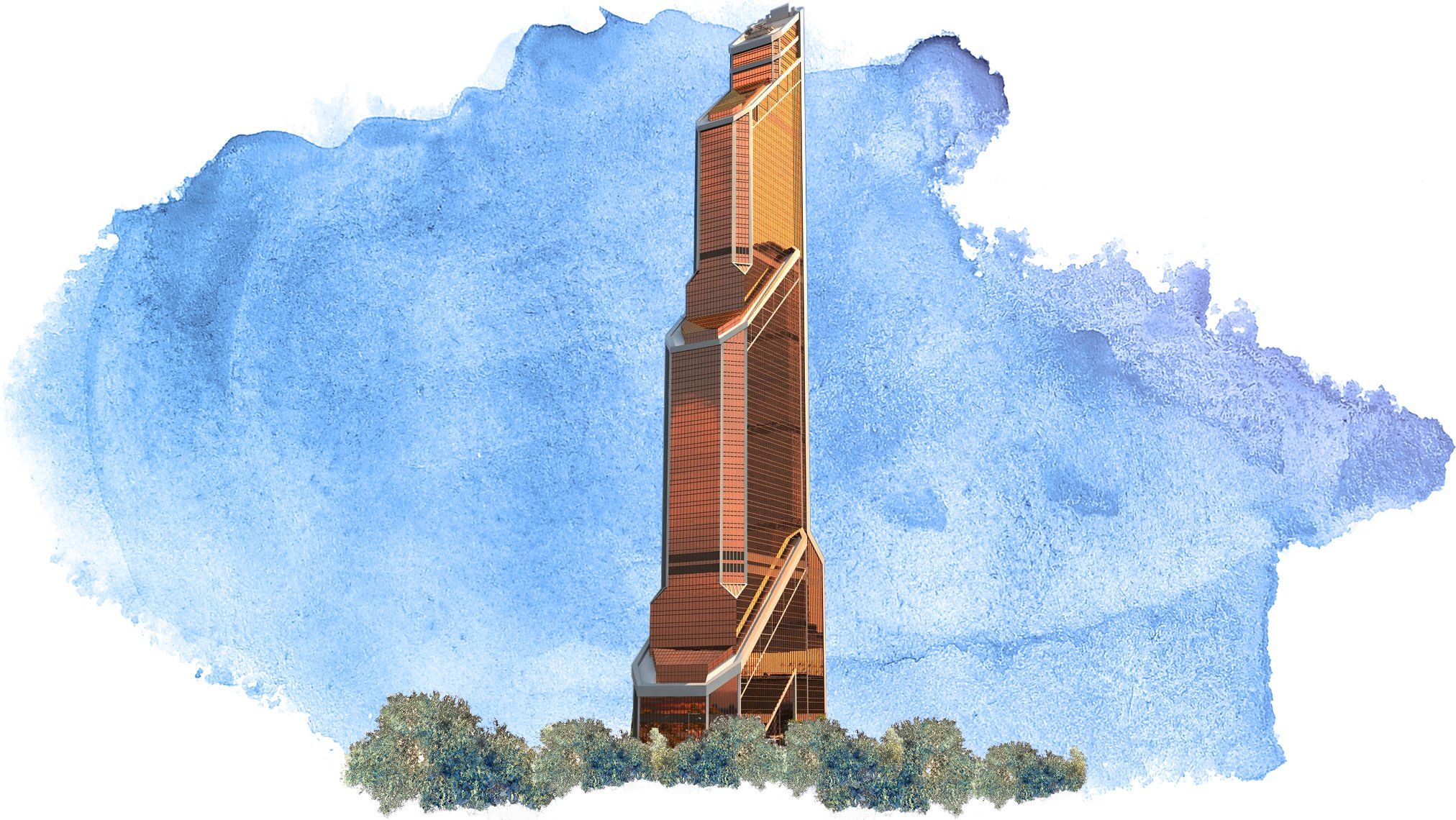
Начало проектирования АДКГ-20 — ТДА с вертикальным разъемом корпуса и повышенной производительностью. В период 2008-2012 гг. на ключевые промыслы страны поставлено в общей сложности 89 агрегатов АДКГ-10.
Начат выпуск АДКГ-20. С 2012 по 2016 гг. будет поставлено 30 агрегатов, а в общей сложности за 2013-2020 гг. отрасль получила 54 турбодетандерных агрегата, приспособленных для работы с газом, характеризующимся большим содержанием парожидкостной фазы.
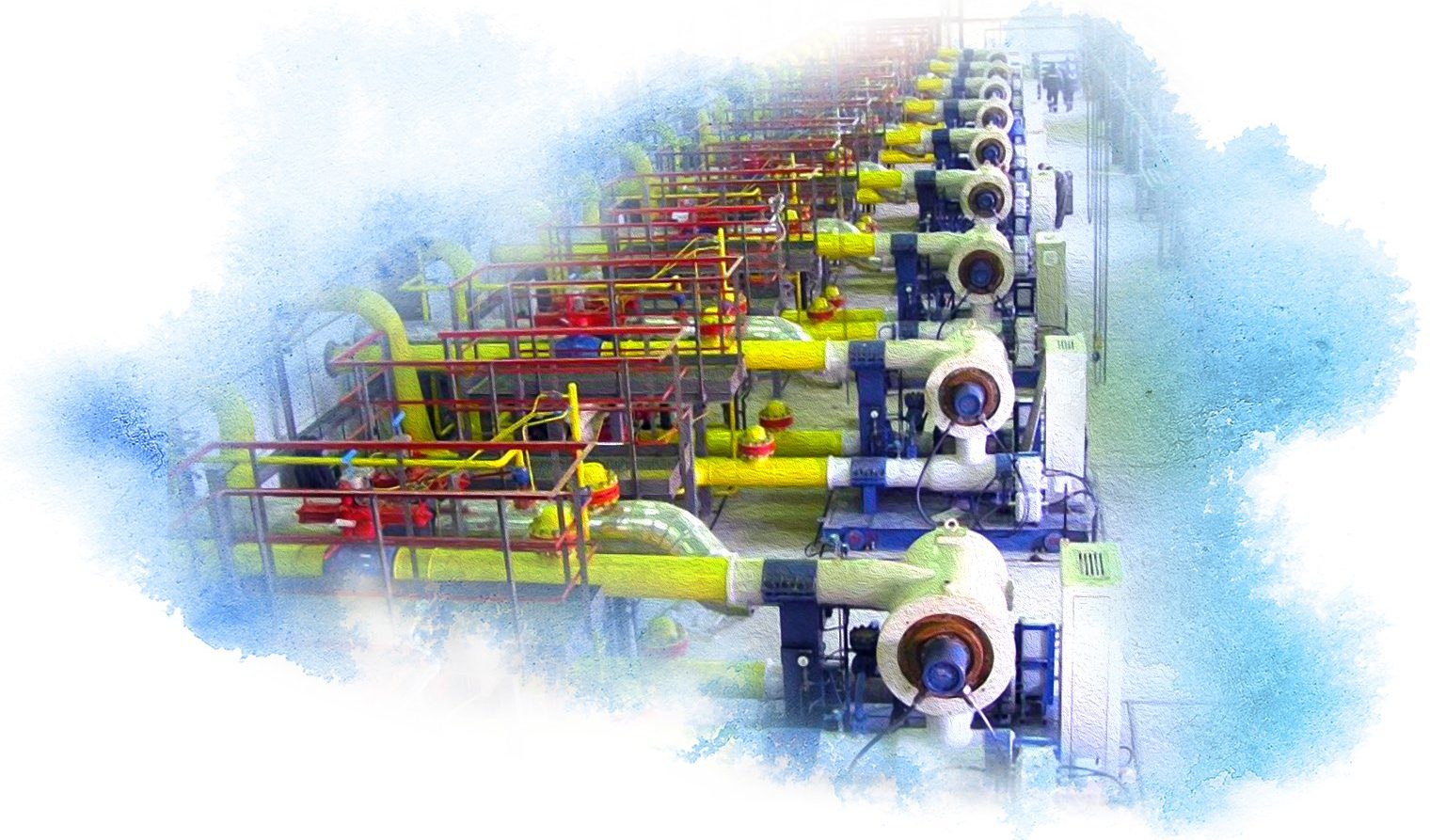
Инициирована разработка комплексных ресурсосберегающих решений на базе турбодетандерного агрегата, в том числе для выработки чистой электроэнергии. Компания продолжает активно развиваться во всех проекциях: конструкторской, технологической, корпоративной. Идет реструктуризация и оптимизация производства, создается Центр компетенций, внедряются аддитивные технологии.